Physical vs. Virtual / Simulation Tests: Unveiling the Synergy of Product Development
- Mohamed Abdelmomen
- Jun 29, 2023
- 3 min read
Introduction
In the ever-evolving field of mechanical engineering, the development and testing of physical products play a crucial role in ensuring their performance, reliability, and safety. Traditionally, physical testing has been the go-to method for evaluating product performance. However, with advancements in computational power and simulation technologies, virtual testing or simulation has emerged as a viable alternative. In this blog, we will explore the realm of physical and virtual/simulation tests for physical products, highlighting their respective advantages, limitations, and real-life examples.
I. The Power of Physical Testing

Physical testing involves subjecting a physical prototype or product to real-world conditions, measuring its performance, and analyzing its behavior. This method has long been relied upon by engineers for its tangible and direct evaluation of a product's characteristics.
Here are some key advantages of physical testing:
1. Authenticity
Physical testing provides the most accurate representation of a product's performance since it operates under actual operating conditions, allowing for real-time data collection and analysis.
2. Real-world Verification
Physical tests verify the theoretical assumptions made during the design phase and assess the product's ability to meet functional requirements and regulatory standards.
3. Failure Analysis
Physical testing enables engineers to understand failure modes, identify weaknesses, and make necessary design improvements to enhance product durability and reliability.
Real-life Example 1: Automotive Crash Testing
One of the most notable applications of physical testing is in the automotive industry. Crash testing involves simulating real-life accidents to evaluate a vehicle's structural integrity, occupant safety, and overall crashworthiness. By conducting physical tests with dummies and instrumented vehicles, engineers can measure impact forces, analyze deformation patterns, and optimize vehicle designs to enhance passenger safety.
Real-life Example 2: Material Strength Testing
Physical testing is also invaluable for determining material properties and structural strength. For instance, tensile tests assess a material's ability to withstand tension forces, allowing engineers to characterize its strength, ductility, and failure points. Such tests aid in material selection, structural design, and ensuring product longevity.
II. The Advantages of Virtual / Simulation Testing
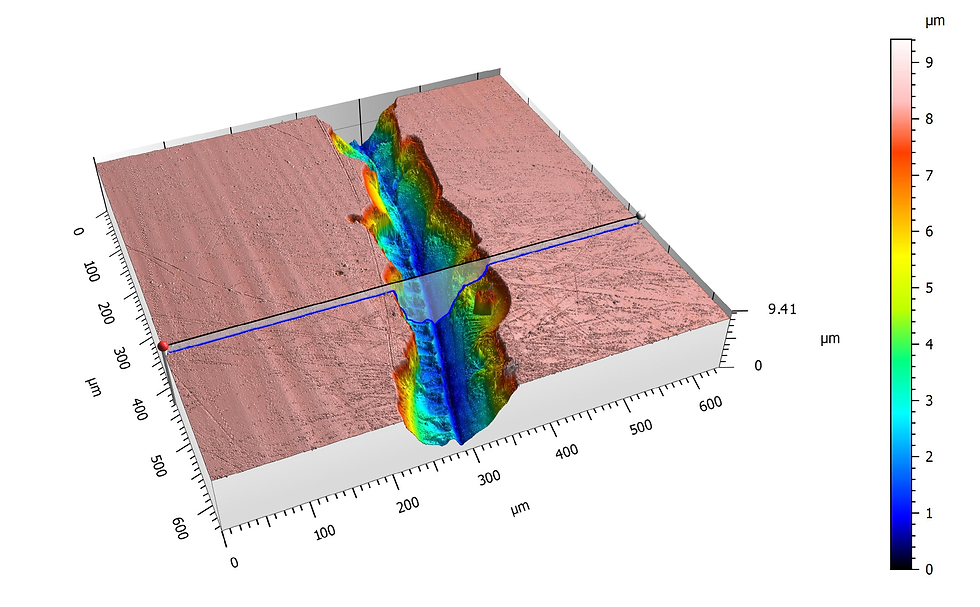
Virtual or simulation testing involves creating computer models that simulate the behavior of physical products under various conditions such as: Ansys, Abaqus, MSC Adams, Nastran, Solidworks, MATLAB, COMSOL, CREO, Siemens NX, and Visual Components. These digital models leverage complex algorithms and numerical methods beside topolgy to predict product performance and fitting.
Here are some key advantages of virtual/simulation testing:
1. Cost and Time Efficiency
Simulation testing significantly reduces the time and cost associated with physical prototyping and testing. It allows engineers to evaluate multiple design iterations virtually, optimizing the product before physical prototypes are built.
2. Design Exploration
Simulation enables engineers to explore design variations and test "what-if" scenarios without the need for physical changes. This flexibility facilitates rapid design optimization and innovation.
3. Safety Constraints
Virtual testing allows engineers to evaluate products under extreme conditions or dangerous environments without risking human lives or costly physical setups.
Real-life Example 1: Finite Element Analysis (FEA)
Finite Element Analysis is a widely used virtual testing technique. It involves dividing a complex structure or product into smaller, simpler elements, allowing engineers to simulate its behavior under different loads and boundary conditions. FEA helps identify areas of stress concentration, optimize material usage, and predict failure points, ultimately leading to improved product performance.
Real-life Example 2: Computational Fluid Dynamics (CFD)
CFD simulations are employed to study fluid flow behavior, heat transfer, and aerodynamics. Industries such as aerospace and automotive extensively use CFD to optimize the shape of objects, improve fuel efficiency, reduce drag, and enhance thermal management.
III. The Synergy: Combining Physical and Virtual Testing

While physical and virtual/simulation testing each offer distinct advantages, the true power lies in combining these approaches to achieve comprehensive product evaluations. By integrating physical and virtual tests, engineers can benefit from the strengths of both methodologies.
Here are some synergistic applications:
1. Validation and Verification
Physical tests can be used to validate simulation results, ensuring that the virtual model accurately represents the real-world behavior of the product. Conversely, simulations can complement physical tests by providing insights into unmeasured parameters or complex phenomena that are difficult to capture experimentally.
2. Optimization
Virtual testing allows engineers to quickly explore a vast design space, narrowing down the potential options before proceeding with physical prototyping and testing. This iterative process optimizes product performance while reducing development time and costs.
3. Failure Analysis and Safety Enhancements
Physical tests provide valuable failure data that can be used to improve simulation models and validate their accuracy. Simultaneously, virtual tests enable engineers to identify critical areas for physical testing, saving resources and increasing safety.
Conclusion
In the realm of mechanical engineering, the choice between physical and virtual/simulation testing should be approached with a synergistic mindset. Both methods possess unique advantages and limitations, and their combination can revolutionize product development. Physical testing offers authenticity, real-world verification, and failure analysis, while virtual/simulation testing provides cost and time efficiency, design exploration, and safety constraints. By harnessing the power of both approaches, engineers can create better-performing products that meet or exceed customer expectations while reducing development time and costs. Embracing the synergy between physical and virtual/simulation tests is the key to unlocking innovation and driving the future of mechanical engineering.
Comentarios